A company abreast of the times
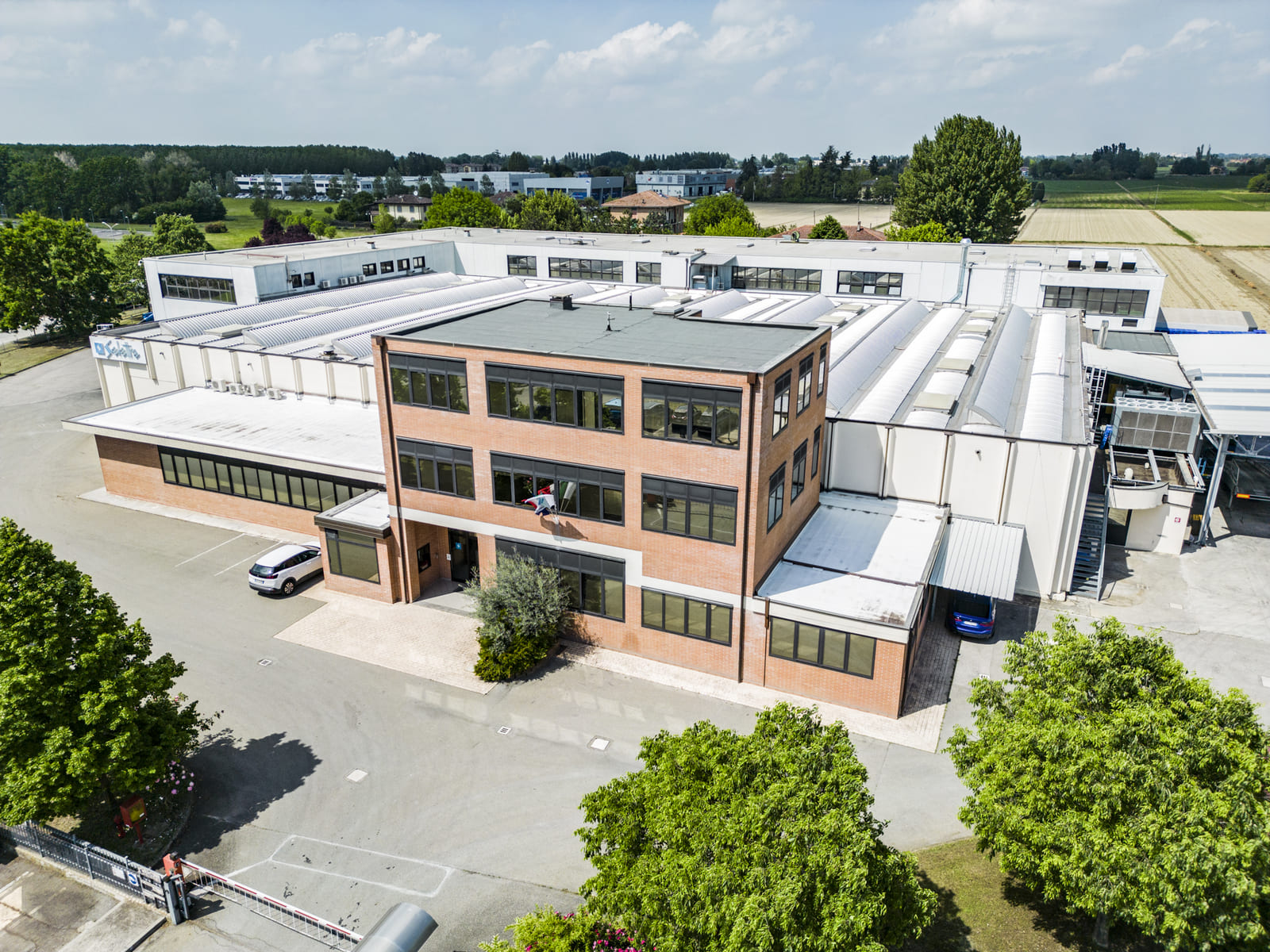
A story that began way back
Ours is an Italian company that has been designing and manufacturing components for engines and micromotors for over 45 years.
Backed by our experience, we can offer extremely reliable, technologically advanced products compliant with the highest safety standards.
1978
Selettra was established in Castelmaggiore for the purpose of designing and manufacturing complete ignition units for internal combustion engines
2003
After moving twice, we enlarged both the electronic department and the offices of the Bentivoglio facility
2008
Investments were made in new robotic lines for application of mechanical finish machining processes to magneto flywheels
2010
The light aluminium alloy die-casting work was brought in-house
Oggi
We now invest in technologies to achieve increased productivity, competitiveness and the highest possible quality level through automation
Each year we produce
5.000.000
Flywheels
100.000
Ignition units
20.000
Rotors
Core sectors
Our products are mainly used in the following sectors: gardening and maintenance of green spaces, go-karts, motorsports, RC model building, paramotors, outboard and ultralight motors.
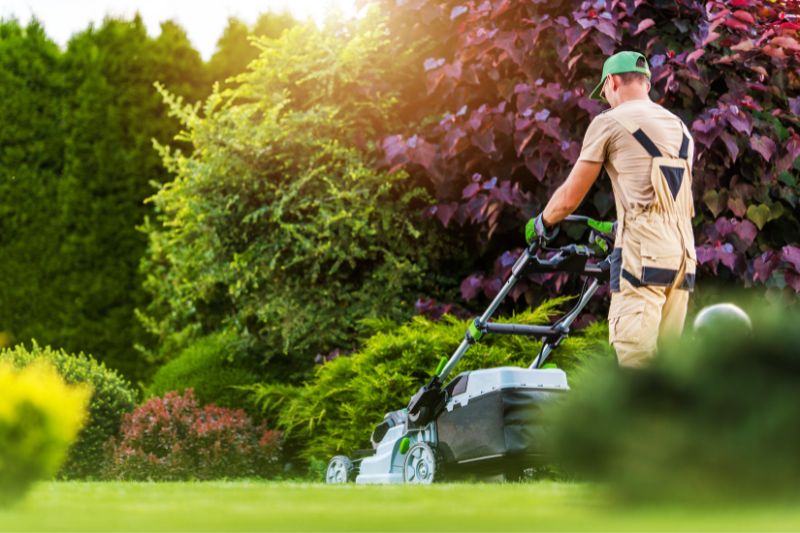
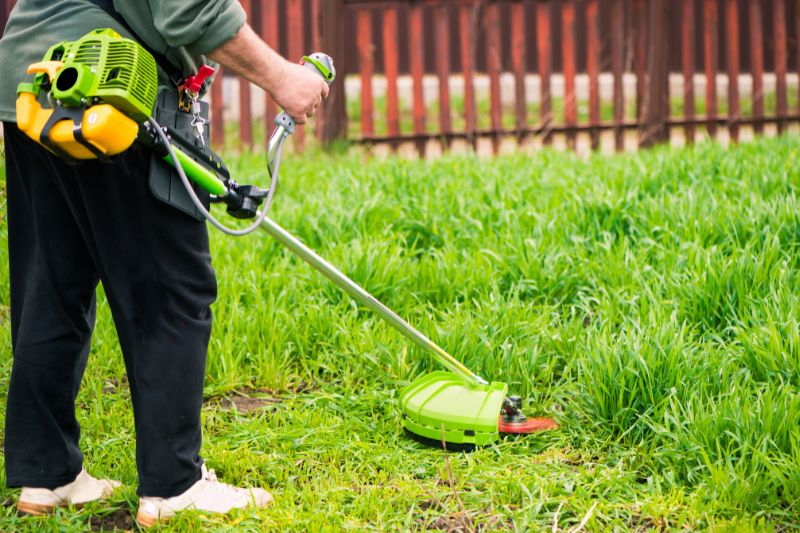
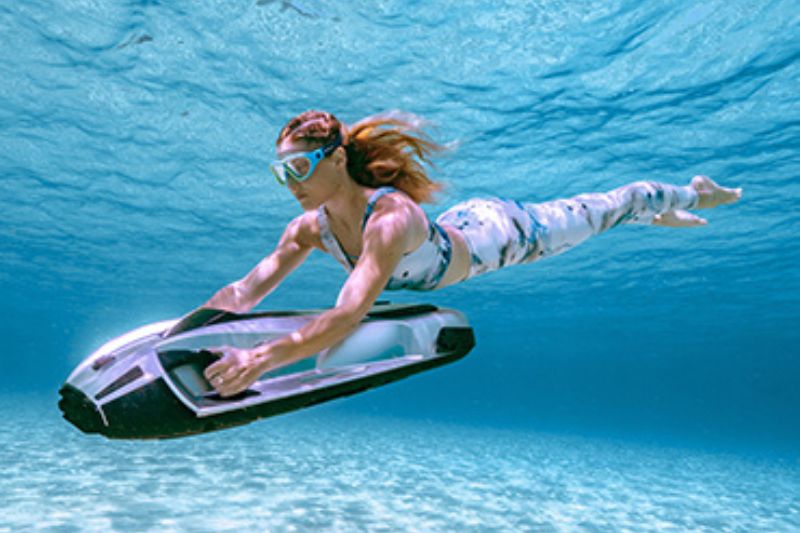
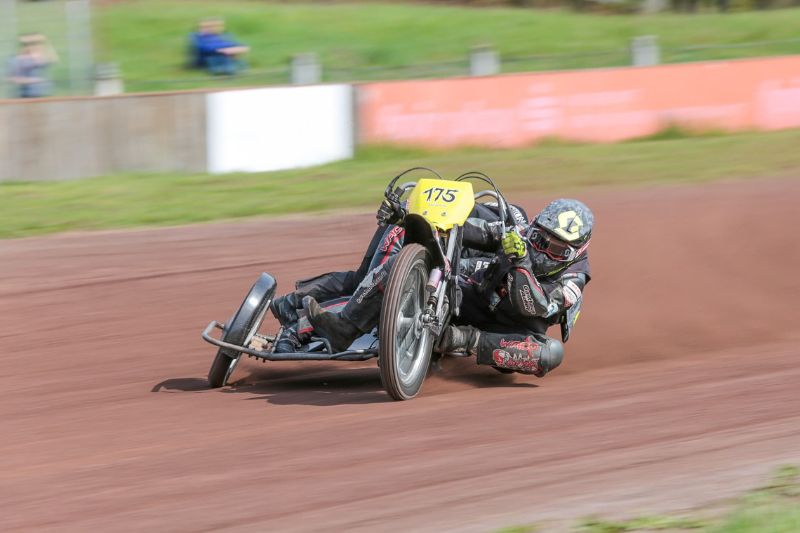
“Made in Selettra” go-kart ignition units are CIK-FIA type-approved for participation in international races and competitions.
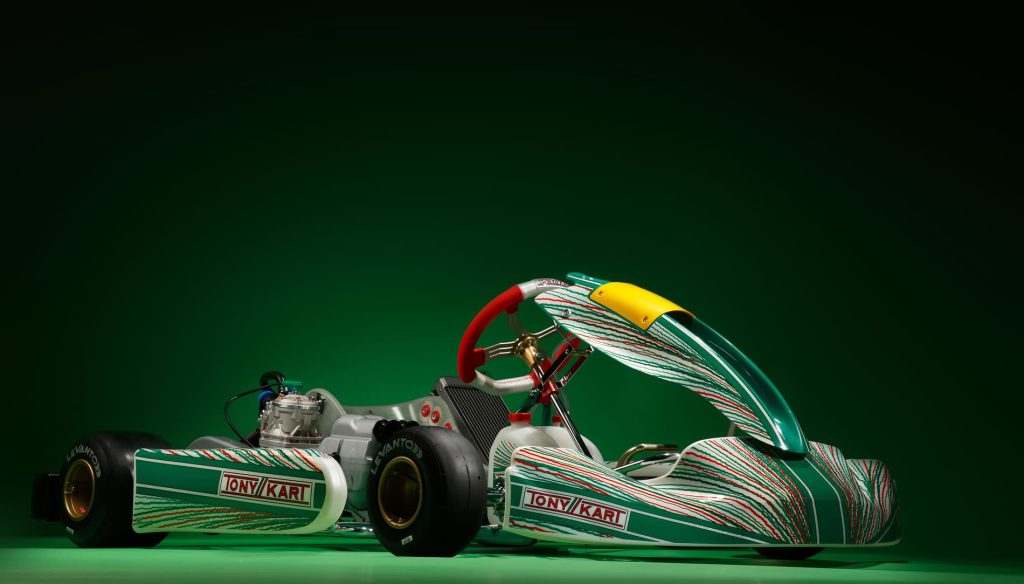
Your project?
Our next challenge
Integrated innovations for optimized processes
We make regular investments in highly technological robotic applications which enable us to:
01 / Increase the quantity of products we manufacture
02 / Meet the specifications requested by our customers
03 / Provide thorough and accurate quality control
04 / Reduce the lead times for customized articles
A forward-looking strategy
Our production facility provides for the integration of specialized industrial machinery in every department.
Our foundry employs advanced technology able to support every stage of the production process.
Here, optimized operating efficiency guarantees constant precision throughout our processes.
- Italpresse and Colosio machinery and systems
- 6 (six) 400- to 750-ton capacity presses
- Complete control of the machine parameters integrated into the management system
- 5 anthropomorphic robots for loading inserts into the die
- 5 anthropomorphic robots for unloading shots
- Rotary tables for cooling die-cast shots
To provide customers with high quality final products, the blanks are precision-processed in the mechanical finish machining department.
- 6 stand-alone workstations providing specific mechanical machining processes for magneto flywheels. From turning to balancing and magnetizing
- conventional horizontal lathes
- numerical control lathes
- vertical lathes
- thread-cutting machines
- column drills
- broaching machines
- balancing machines
- magnetizers
- Hydraulic presses for removing aluminium castings from the sprues
Cutting-edge instruments in our quality control department define our commitment to providing impeccable, safe products. The department is outfitted with equipment able to guarantee that every component is made from superior quality materials.
- Spectrometer for OBLF alloy analysis
- Hysteresisgraph for controlling magnets
- Zeiss coordinate measuring machine (CMM) for dimensional checks
- Digital microscope
- Roughness tester
- Bosello Zeiss industrial X-ray system
- Gilardoni industrial X-ray system
- Balancing machines
- Burst test unit